Are you wondering why Porcelain Tiles are the most popular tiles in the world? What makes glazed porcelain tiles so much in demand and how is it made? Porcelain tiles have been manufactured around the globe for hundreds of centuries. They are most widely used on floors and walls due to their unique features, benefits, and versatility.
While you are exploring a different range of porcelain tiles for your residential or office project, we want you to take a few minutes and understand the entire process involved in manufacturing glazed porcelain tiles.
Also, do you know that porcelain tiles can replicate stone, marble designs, and wood? Being the leading Glazed porcelain tiles manufacturer in India, AsiaTrade Ceramika and its team of product engineers practice a well-aligned and industry-approved process to manufacture glazed porcelain tiles. So let us begin to understand.
Why Choose Glazed Porcelain Tiles for Your Project?
Glazed porcelain tiles are created from a distinguished quality of clay burnt at high temperatures, eliminating moisture and creating a firmer grip and thickness. They have the least water absorption rate which is less than 0.5%. And that is why, they are thicker and long-lasting. Moreover, glazed porcelain tiles 600X1200 mm come with an extra layer of glaze that adds beauty and elegance to your space, keeping the room brighter and shinier. The manufacturing process makes porcelain tiles tougher and sturdier to withstand heavy traffic. They have reduced porosity and can sustain their technical qualities for a longer time. The below process is the most advanced and modernized production process to make glazed porcelain tiles.
Manufacturing Process of Glazed Porcelain Tiles
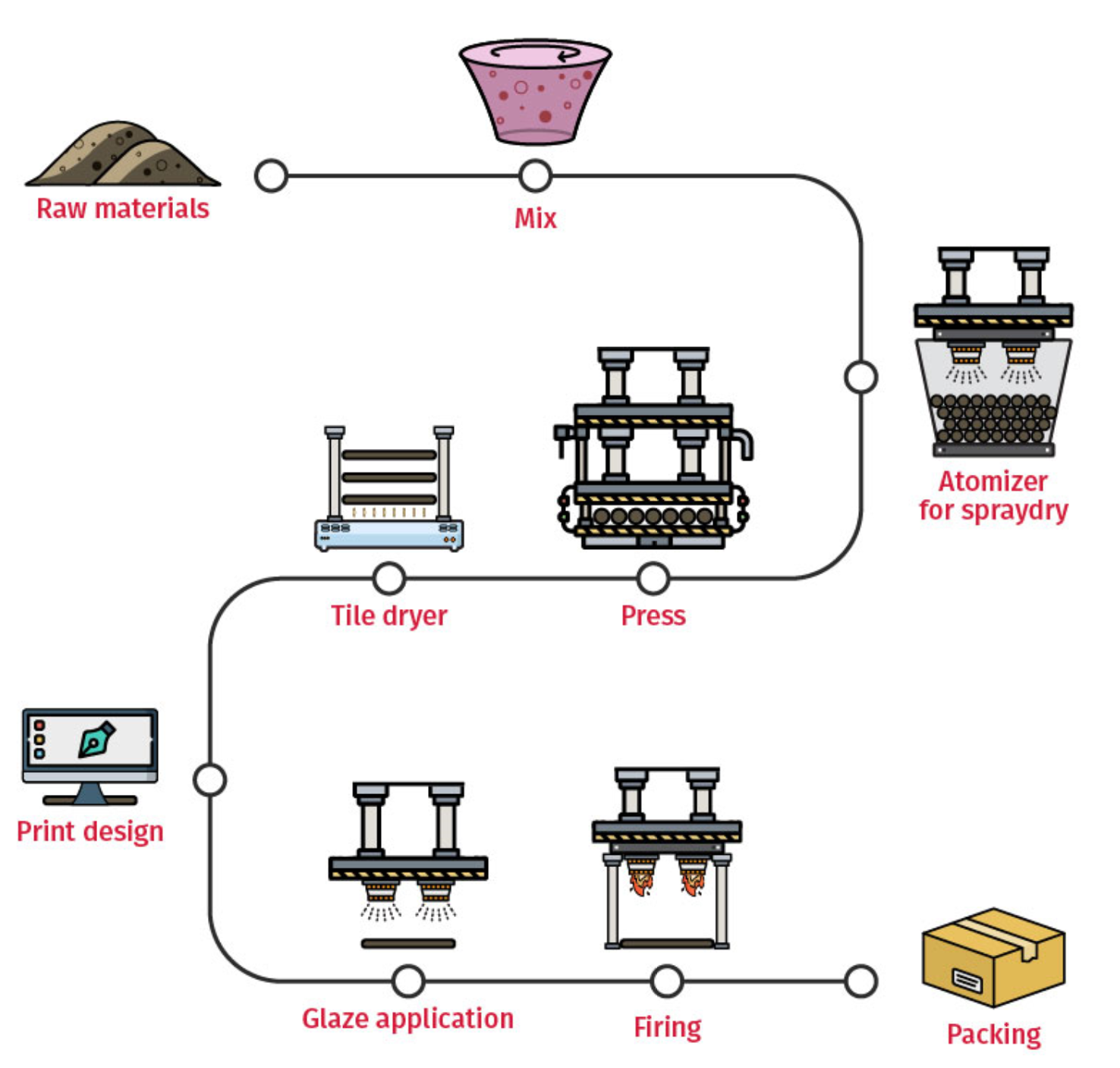
In the present times, tile manufacturers all over the globe are adopting newer techniques and methods to produce porcelain tiles. They have changed the outlook and quality of tiles by updating designs, production processes, and technologies. For over a decade, we have been manufacturing glazed porcelain tiles and understand the importance of following the process and techniques to make them durable and stronger. Are you interested in knowing the process of making these tiles? Below are the steps listed with a detailed explanation of how it happens.
Batching
Most of the porcelain tiles differ due to the quality and nature of the raw materials used. The body composition of various tiles differs, influencing their colors, hardness, and other tile body properties. To get the desired quality, you must carefully blend the ingredients in the prescribed proportions. An ideal raw material combination can be acquired by using batch calculations, helping in determining the exact weight of each raw ingredient that should be used.
Mixing and Grinding
After taking all the proportionate raw materials like sand, clay, silica, feldspar, and others, they are mixed into a huge mixer that is called a ball mill. The mixing process is done by adding water in proportionate quantities. To get the finest texture of the tiles, either ball stones or alumni pebbles are added to the ball mill. The end product of this water-filled slurry is named slip.
Color Mixing
Various ceramic colors are added to the slip, creating diverse colorful bodies. The mixture is then added to a high-speed blender tank. This procedure is optional and can be eliminated if only basic body color is needed. Many customers love the natural shades of ceramic and therefore these shades are always available in the collection.
Spray Drying
All the extra water from the slip is removed through the spray drier. The slip is then pumped into an atomizer that has nozzles. This is one part of the procedure. Gradually the slop droplets get heated by increasing hot air and the moisture evaporates. Finally, the liquid slip becomes a fine powder.
Creating the Tile
The dried slip powder is further processed through dry pressing. The slip powder is dried in a forming die, creating tiles. Tiles are created after giving around 75000 tonnes of pressure to a steel plunger, compressing the material phenomenally. The aim of this process is to create a dense and less porous ceramic mass. Further, this mass is fired at higher temperatures to produce a stealthier and stronger body that can absorb very little water.
Drying
In the next process, the pressed ceramic mass that is now converted into a raw tile is further sent for the drying process. Through this process, any sort of extra moisture gets eliminated before firing, avoiding shrinking fractures in highly humid environments.
Printing and Glazing
The next stage is printing and glazing. A hi-tech laser inkjet printing and patterns machine is used to cover the body color of the tile. At this stage, the manufacturer can give the desired color, effect, and texture to the tiles soon after they are laid for drying. Through this process, the tiles become stain-resistant and develop a unique pattern that adds beauty and improves grace. Further, a glazed material layer is added on top of the color and design, making it more decorative, glossy, and moisture-resistant. At this stage, the tiles are almost done with most of the process and you will see them look shinier and finished. But that is not all!
Firing
Now the time is to fire the tile in a roller kiln at a high temperature of around 1200 degrees Celsius. With this process, the soft clay inside the tile will also become firmer, non-porous, and resilient, improving the glaze and shine. All the remaining moisture will now completely vanish due to the high temperature. However, the firing time and the amount of heat applied to tiles differ based on the size of the tile.
Polishing and Squaring
At this stage, most of the tiles go for further polishing. They are polished and honed, making their surface look glossier, shinier, and attractive. Mostly, glazed porcelain tiles are polished to a lappato surface or a glossy finish by using different kinds of abrasive instruments. Based on the patterns and design elements, the edges may be corrected or left unrectified to give a natural look. In the process of rectification, the edges of tiles undergo cutting or grinding to give a consistent design with very few variances, ensuring installation convenience.
Selection and Packing
The last step before the tiles are shipped is packing. Before packing, each tile gets graded according to its flatness, appearance, hues, size, and dimensions. Thereafter, they are labeled, organized, and packed in boxes.
Conclusion
Manufacturing glazed porcelain tiles is a challenging process. We hope the above explanation will give you better insights about the tile creation journey. And we also hope now you understand the process and what it takes to get the glazed shine. Imperial Ceramics is the leading Glazed porcelain tiles exporter, delivering state-of-the-art tiles to various countries across the globe. Over the years, we have provided our customers with a variety of premium quality glazed porcelain tiles. Check out our range of collections here and learn more about our products.